Die stille Revolution im Emder Volkswagenwerk
Die Öffentlichkeit sieht nur die neuen Stromer, doch intern trimmt VW sein Werk auf Umweltschutz und Einsparung. Die Wege vom Zulieferer bis zum fertigen Auto sollen kürzer werden - und wenn das nicht geht, dann wenigstens per Bahn zurückgelegt werden.
Lesedauer: ca. 2min 12sec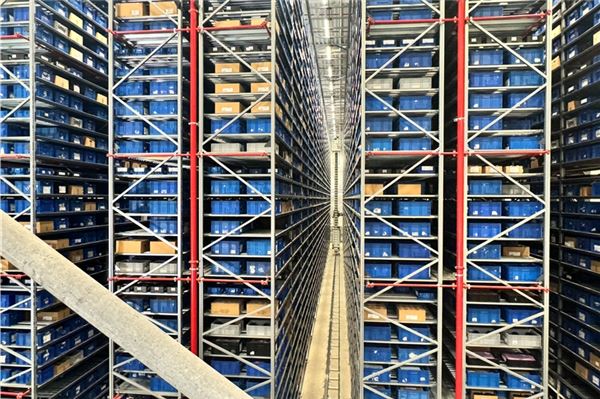
Das neue zentrale automatisierte Hochregallager ersetzt viele andere kleine Lagerflächen. Es bietet Platz für 86000 Lager-Boxen – für Groß- und Kleinteile. ©
Emden Die Revolution nach außen kann jedermann sehen: Das VW-Werk spuckt Elektro-Autos aus statt Verbrenner-Modelle. Unvorstellbar 1,3 Milliarden (oder 1300000000) Euro hat der Konzern ins Emder Werk gesteckt. In dieser Summe verstecken sich 334 Millionen Euro für die Verbesserung der Logistik. Seit 2018 läuft das Projekt.
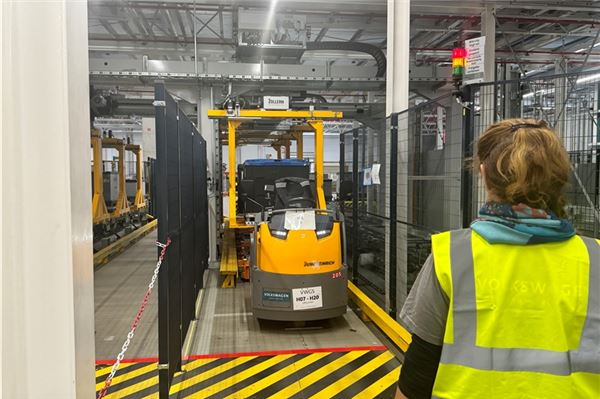
Übergabe von Boxen mit Teilen auf einen Transportzug. Künftig soll er sogar fahrerlos bis zur Montage fahren. ©
Von dieser stillen Revolution bekommt der Kunde allerdings nichts mit. Ihr Ziel: CO2-Reduzierung, Kosteneinsparung, Einsparung von Arbeitsplätzen und höhere Verlässlichkeit in der Logitikkette.
Karte
Die Einzelprojekte:
Anlieferung per Bahn statt Lkw
Erreichten bisher jeden Tag 170 Lkw das Werk mit Kfz-Teilen aus ganz Deutschland das Werk, sind es künftig nur fünf Güterzüge. Sie werden zentral in Dresden beladen. Bereits seit 2018 wird das System aufgebaut und funtioniert inzwischen reibungslos. Es spart 10000 Tonnen CO2 pro Jahr und reduziert den Lkw-Verkehr um 75 Prozent. Auf die Bahn mochte sich VW für dieses Projekt nicht verlassen: Es engagierte dafür SmartRail, ein Joint-Venture der Spedition L.I.T. aus Brake und Captrain aus Frankreich.
Neues Hochregallager
Rund 42 Millionen Euro hat VW in ein neues Hochregallager direkt neben der Produktion investiert. Es ersetzt mehrere dezenrale Lagerstätten in Emden, vermeidet jeden Tag 74 Lkw-Touren und damit 123 Tonnen CO2 jährlich. Die Einlagerung der in Boxen verstauten Teile erfolgt computergesteuert. Ebenso die passgenaue Auslieferung ins Werk. Nebeneffekt: Bei externen Dienstleistern (Dirks Group, Spedition Weets und VW Group Services) entfallen 170 Arbeisplätze.
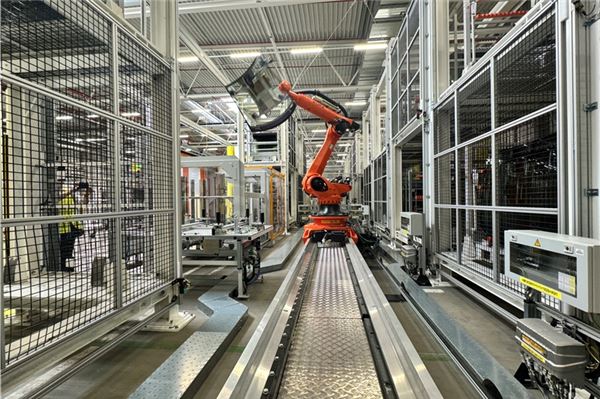
Schwere Windschutzscheiben werden per Roboter kommissioniert. ©
Die papierlosen „Supermärkte“
Klingt etwas skurril, aber spart zwei Tonnen Papier im Jahr. Im Werk – zwischen Hochregallager und Produktion, gibt es Sammelstellen für Einzelteile, aus denen je nach Produktion die richtigen Einzelteile entnommen werden. Beispielsweise der genau richtige Außenspiegel. Früher ratterten hier Bestelllisten über Nadeldrucker. Inzwischen werden die Infos auf ePaper-Bildschirmen angezeigt.
Weniger Plastik bei der Verpackung:
Das Teilprojekt heißt „No Plastic“ und auf einen Privathaushalt übertragen bedeutet es soviel wie: Überflüssige Verpackungen weglassen. 22 Tonnen Plastikmüll wurden beispielsweise 2023 eingespart. Einzelteile, beispielsweise
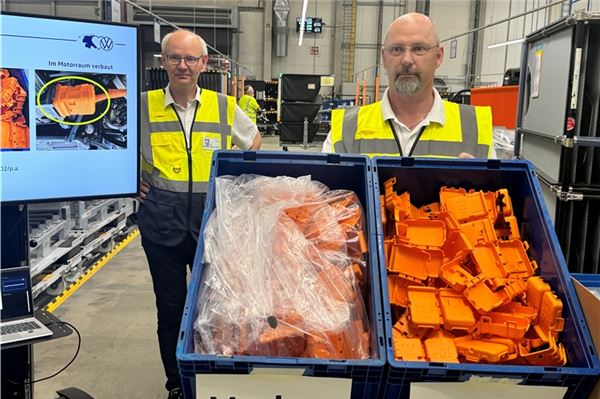
Vorher: Viel Plastik, nachher: weniger Plastik. Auch Teil der VW-Strategie. ©
Die Bereitstellung von Glasscheiben
Dieses Projekt hat ausschließlich das Ziel, Mitarbeiter von schweren Tätigkeiten zu entlasten: Die bis zu 15 Kilogramm schweren Windschutzscheiben werden vom Roboter aus den großen Lieferboxen geholt und dann direkt ans Band geliefert.